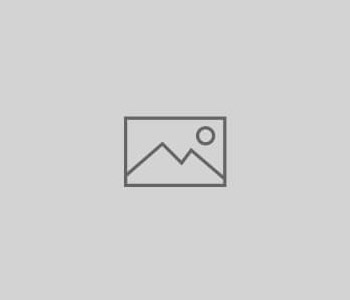
Design
Some of our design work includes:
- Value-added engineering
- Temporary access
- Soil shoring and cofferdam systems
- Lift plans
- Pile-load testing
- Steel fabrication
- Heavy equipment mobilizations and logistics
- Consolidation grouting and annular grouting