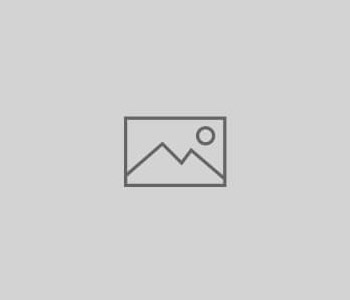
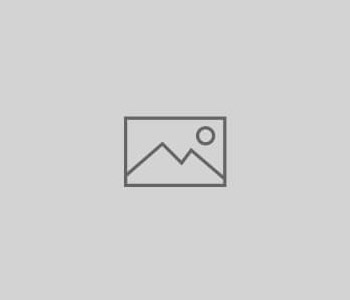
Key Stats:
The project was completed without safety incidents and complied with all local regulations, employing significant local labour.
The Pandora project consisted of multiple scopes of work for western grater including blasting, shotcrete shoring and tie-back anchors. The shotcrete shoring system consisted of H piles drilled in from the surface, horizontal whaler beams and tie-back anchors to further support the vertical shotcrete wall. Traditional blasting methods were used to complete excavation to the desired depth.
Like many sites on Vancouver Island, rock is rarely far away. The Proxima is situated almost entirely on solid bed rock, requiring quite a bit of blasting for Western Grater to achieve the desired depth to allow for ample off-street parking in two levels of underground parkade. Shoring Along the Lampson Street property line consisted of 4” pipe piles and tie back anchors to achieve a safe vertical shoring wall, and to maximize the full extent of the property.
The Proxima is Located on the corner of two very busy streets (Lampson St. and Esquimalt St.) including a busy intersection. Like most Urban blasting operations great care was taken to ensure the safety of the public and surrounding structures while attempting to minimize the impact on the neighboring community.
The majority of the Aura project is blasting as two large mounds of rock mounds with a central valley encompass the site. An older road stabilization lock block wall spans the valley which requires Shotcrete Shoring to support the wall as the excavation extends below the base of the wall. The unstable nature of the local rock formations requires rock fall mesh to ensure worker safety while foundation works occur
Located in a small residential area, road access to the Aura proved to be quite a challenge. Western Grater and the other contractors on site worked closely with the neighbours to minimize the negative impact on the neighbourhood. Blast mats were used to prevent fly rock and to mitigate any potential damage to surrounding homes and structures.
The scope of work on the Langshire project was mainly blasting but due to local conditions WGC also drilled and installed rock bolting and some shotcrete to secure loose rock and unstable geological formations.
The Westshore Parkway in Langford hosts many other neighbouring commercial buildings including some in active construction. Large-scale blasting in semi-urban conditions produces many challenges for the team as there are many potential hazards to watch for, including many construction workers and their equipment in the blasting area. Great care was taken to ensure open communication with surrounding trades to make sure everyone goes home at the day safe and happy every day.
Western Grater Maintains a fleet of Epiroc Flexiroc Hydraulic rock drills, which are utilized to drill 4” diameter holes ranging from 25’ to 50’ deep. Blast sizes vary a fair amount ranging from 80 to 300 holes per blast. Due to the size of the blasts, covering the shot with blast matts is not feasible therefore great care is taken while loading to ensure all rock remains in the blasting area. The blasted rock is then transported with excavators and rock trucks from the blast area to the crusher where it is crushed to various sizes for various uses.
As a rock quarry Center Mountain is governed by the Ministry of Mines rather than WorkSafe BC as most of our other blasting operations are. WGC has offered extensive training to our most qualified blasters to obtain their Mines Blasting Certification and to maintain stringent safety procedures for loading and guarding. Western Grater holds one of the highest safety records in the business.
This Project consisted of multiple scopes of work for Western Grater including blasting, shotcrete shoring, and tie-back anchors. The shotcrete shoring consists of welded wire mesh and rebar to reinforce the shotcrete creating a stable vertical wall allowing developers to maximize land utilization. Tie-back anchors are drilled and grouted to further support the shotcrete wall system. Western Grater utilizes a hollow anchor bar system which greatly improves efficiency over traditional drilling methods.
Blasting works occurred over a 3-4 month period with a total rock volume of over 8900 cubic meters. Due to the extremely close proximity of the neighbouring heritage building, a “line drilling” method was used to ensure an accurate rock break at desired property line.
As with most blasting operations in urban settings, much care must be taken to ensure the safety of all other workers and the general public, as well as the presence of older structures from the early 20th century that the city of Victoria is famous for. On the Spencer Block project there is an adjacent brick building built in 1908 by Sam Kee Laundry, the utmost care was taken to ensure no damage was sustained and the impact to the residents was kept to a minimum. Engineers are also involved in the monitoring of neighbouring structures to ensure all excavation perimeters remain stable and safe.
Another major challenge on this project was the local ground conditions. Due to poor environmental practices in the early 20th century, large areas of the job site contained contaminated soil at depth. The presence of this contamination creates challenges for all contractors involved, such as removal of contamination, which comes with great cost to the client and delineation of materials for the excavation contractor. These conditions also create some hurdles for WGC as the ground conditions were not conducive to bonding anchors to soils. WGC employed the use of a “grout Swivel” which allows us to drill anchors in with continuous grout flow throughout the drilling process as opposed to the traditional method of drilling with air and grouting post installation. The use of this method provided great success upon its application.